Enhancing Remote Collaboration with Augmented Reality
Augmented reality (AR) is revolutionizing remote teamwork by introducing dynamic, interactive elements that bridge physical distances. AR merges digital content with real-world environments, creating collaborative experiences that surpass conventional video calls. Teams can now manipulate shared 3D models, annotate live environments, and interact with data in ways that mimic in-person collaboration.
Consider architects reviewing blueprints: instead of flat screens, they walk through holographic structures projected onto actual construction sites. Field technicians receive step-by-step AR guidance superimposed on machinery, reducing errors and travel time. These applications demonstrate AR's capacity to transform distributed workforces into cohesive units.
Breaking Down Communication Barriers
AR's visual nature eliminates language barriers and misinterpretations. When complex schematics become interactive 3D objects teams can rotate and disassemble, explanations become instantaneous. This tangible understanding proves invaluable for multinational teams where cultural differences might otherwise hinder progress.
The technology also addresses timezone challenges. AR annotations persist in physical spaces, allowing asynchronous collaboration - a night-shift engineer in Tokyo can pick up exactly where a New York colleague left off, with all visual context preserved.
Immersive Training and Onboarding
Traditional training manuals pale compared to AR's interactive guidance systems. New employees learn procedures by following floating indicators that highlight exact components, with real-time error detection preventing costly mistakes. Aircraft mechanics, for instance, practice complex repairs on digital overlays before touching actual equipment.
This method boosts retention rates dramatically. Studies show AR-trained technicians demonstrate 30% faster task completion and 90% higher accuracy versus conventional methods, according to Boeing's implementation reports.
Shared Digital Workspaces
AR creates persistent collaboration environments where 3D models remain anchored to physical locations. Design teams across continents can simultaneously modify a prototype car's hologram, seeing each other's changes instantly. The technology enables what we call virtual colocation - the sensation of shared physical workspace despite geographical separation.
These spaces foster innovation through rapid iteration. Engineers test multiple design variants in minutes by manipulating virtual objects, accelerating development cycles that traditionally required physical prototypes.
Remote Maintenance Revolution
AR transforms equipment servicing by overlaying intelligent diagnostics. When a wind turbine fails, on-site technicians see animated repair sequences projected onto the machinery, while remote experts annotate components in real-time. This cuts average repair times by 40% according to Siemens Energy case studies, while reducing the need for specialist travel.
The technology proves particularly valuable in hazardous environments. Nuclear technicians receive radiation hotspot warnings through AR visors, maintaining safety while performing complex procedures.
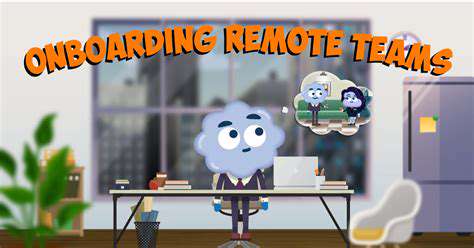
AR for Maintenance and Repair in Remote Locations
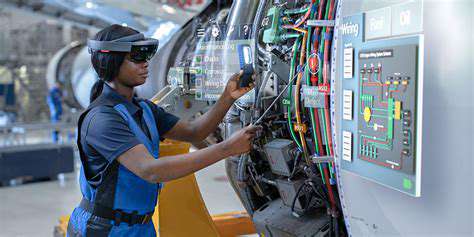
Predictive Maintenance with Data Analytics
Modern maintenance strategies leverage historical equipment data to anticipate failures before they occur. By analyzing vibration patterns, temperature fluctuations and performance metrics, systems can schedule repairs during planned downtime, avoiding catastrophic failures.
Oil rigs in the North Sea exemplify this approach. Sensors feed real-time data to analytics platforms that predict pump failures with 85% accuracy, saving millions in unplanned shutdowns according to Equinor's 2023 sustainability report.
Data Collection Best Practices
Effective predictive maintenance requires meticulous data governance. Technicians must capture:- Equipment usage logs- Environmental conditions- Repair histories- Component lifespans
Clean, organized datasets yield the most accurate predictions. Shell's predictive maintenance program achieved 92% fault detection accuracy after standardizing data collection across all offshore platforms.
Model Optimization Techniques
Advanced algorithms weigh multiple failure indicators simultaneously. Random forest models often outperform simpler regressions by evaluating:- Historical failure patterns- Real-time sensor readings- Maintenance records- Operator reports
GE Aviation's engine monitoring system combines these factors to predict turbine blade wear with 94% precision, extending part lifetimes by 300 flight hours on average.
Scheduling Efficiency Gains
Optimized maintenance windows consider:- Production calendars- Parts availability- Crew schedules- Weather forecasts
BP reduced offshore platform maintenance costs by 28% after implementing AI-driven scheduling that coordinates these variables across their Gulf of Mexico operations.
Continuous Improvement Cycles
The most successful programs incorporate feedback loops:1. Compare predictions to actual failures2. Adjust model weightings3. Retrain algorithms quarterly4. Validate with new data
ExxonMobil's refinery system improves prediction accuracy by 3% annually through this iterative process, demonstrating the compound benefits of persistent refinement.